“We zullen binnenkort veel meer toepassingen van 3D-printing met metaal zien, ook in onze huiskamers”
Onderzoeker Wouter Nuyts onder de loep
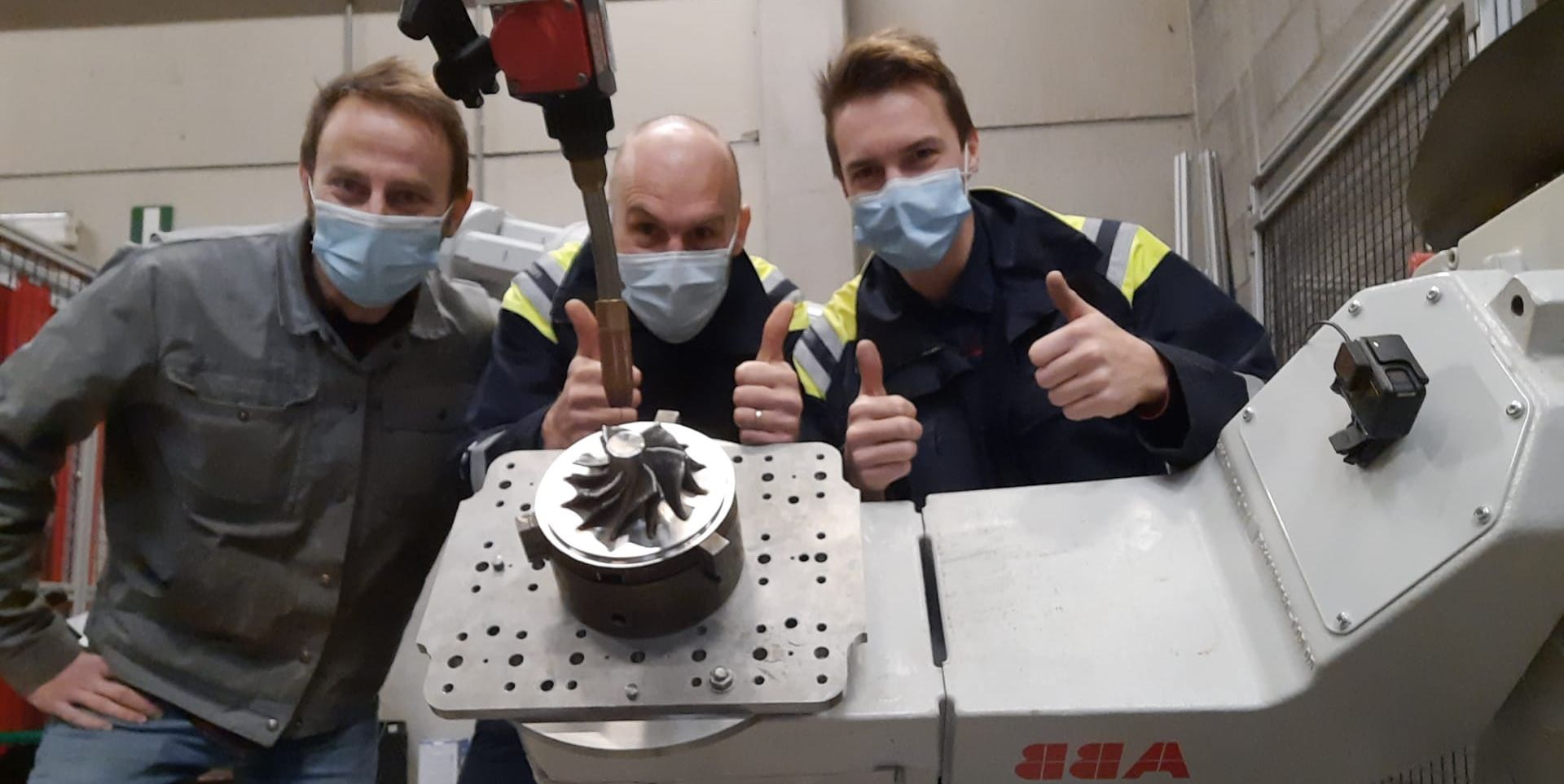
Twee jaar geleden studeerde Wouter Nuyts af in de richting ‘Ontwerp- en Productietechnologie’ aan Campus De Nayer. Meteen daarna kreeg hij de kans om het onderzoek van zijn bachelorproef verder te zetten. Een kans die hij niet liet liggen. “Ik vind het ongelooflijk boeiend om te weten hoe iets werkt, waarvoor de verschillende componenten dienen en hoe alles wordt aangestuurd.”
Een onderzoekende geest, dus. Altijd geweest, zegt hij zelf. Uitzoeken hoe iets werkt en geproduceerd wordt, vormt de basis van zijn onderzoek dat verder helemaal gericht is op het optimaliseren van productieprocessen. Zo nam hij in het recent afgeronde onderzoeksproject, Advanced Processing of Additively Manufactured Parts (Ad-Proc-Add), metaalconstructie en -productie onder de loep.
“We hebben gewerkt met de WAAM-robot, waarmee je laagjes metaal op elkaar kan lassen. Het principe is vergelijkbaar met 3D-printing, maar dan voor metalen en veel grootschaliger. Deze productietechniek vindt toepassingen in o.a. de gas- en olie-industrie, maar ook in machinebouw en autosector. Vaak wordt het gebruikt voor herstellingen. Versleten scharnierpunten, bijvoorbeeld, kan je met de robot terug oplassen en passend maken zodat de machine opnieuw kan worden gebruikt. Maar ik denk dat we in de toekomst veel meer toepassingen gaan zien, ook in onze huiskamers. Precies omdat je met zo’n robot enorm vrij bent in vorm en design. Ik denk bijvoorbeeld aan salontafels. Of een vuurschaal voor in de tuin. Dat soort van architecturale of designtoepassingen behoren echt tot de mogelijkheden. Een Nederlands bedrijf heeft zelfs een complete brug geprint met de WAAM-techniek.”
In de toekomst zullen we veel meer 3D-geprinte metalen objecten zien, in architectuur en design bijvoorbeeld.
Verantwoorde slijtage
Die enorme vormvrijheid is een belangrijke troef. “Wij hebben onder andere een warmtewisselaar gemaakt en een impeller (zie foto). Omwille van die bijzondere vorm een heel interessante case. Maar voor we daar aan toe waren, hebben we zes maanden lang niets anders gedaan dan lijntjes gelegd. En ons telkens de vraag gesteld: ‘Als we een laag leggen met die bepaalde parameter, hoeveel materiaal moeten we dan wegfrezen om een mooie wand zonder onzuiverheden te hebben?’ Want hoe minder materiaal je moet wegfrezen, hoe beter. Niet omwille van het materiaalverlies, dat kan je recycleren. Wel omdat het frezen veel tijd vraagt en hoe meer je freest, hoe sneller de machines verslijten. Daarom wegen we altijd af of de kost van de slijtage verantwoord is ten opzichte van de tijd die we winnen.
Zoals vaak gebeurt, roept een onderzoek nieuwe vragen op, wat aanleiding geeft tot nieuw onderzoek: Ad-Proc-Add 2 staat in de startblokken. “In het vervolgonderzoek gaan we het nabewerken van stukken verder analyseren, maar ook werken met meerdere materialen. Tot nu toe hebben we altijd met constructiestaal gewerkt. Maar we zien dat er in de industrie nood bestaat aan combinaties, om bv. coatings aan te brengen op warmtewisselaars of op oppervlakken die onderhevig zijn aan slijtage. Zo’n buis heeft dan een binnenwand van messing en een buitenkant van staal. De warme vloeistof loopt dan langs de buitenkant en binnenin zit een vloeistof die afkoelt – of omgekeerd. Afhankelijk van de materialen die je gebruikt, gaat die afkoeling sneller en is de uitzetting minder. Daarom willen we testen welke materialen goed aan elkaar gelast kunnen worden.
Digitalisering en van 2D naar 3D
Inmiddels vraagt ook een ander onderzoek zijn aandacht: ‘Digitek 4.0’, over de digitalisering van 2D-ontwerptekeningen. “Neem nu het vergiet dat je gebruikt in de keuken. Dat is ooit gemodelleerd geweest, anders kan je het niet maken. Die tekeningen werden vroeger afgeprint en doorgestuurd naar de productie. Vandaag willen we één bestandsformaat hebben met daarin het 3D-model en alle maten erbij, zodat we voor een productielijn één enkel bestand hebben met alle gegevens van het te produceren object. Daarvoor bestaan verschillende softwarepakketten. Wij onderzoeken wat de mogelijkheden daarvan zijn, in samenwerking met verschillende bedrijven. Aan de hand van wat zij vragen, bekijken wij of die toepassing al dan niet mogelijk is en wat de winsten zijn op langere termijn. Want omdat we alle gegevens in één digitaal bestand hebben, kunnen bepaalde handelingen automatisch gebeuren waar die vroeger manueel moesten worden geprogrammeerd. Op die manier spaar je tijd.”
Naast onderzoeker is hij ook gastdocent in de opleiding waar hij zelf afstudeerde. Wouter (lachend): “Toen werden mijn docenten van vroeger plots mijn collega’s. In het begin was dat vreemd, nu ben ik eraan gewend. Ik geef twee vakken: Eindige Elementenanalyse, over het berekenen van sterkte, en Reversed Engineering, waarin we iets herontwerpen en opnieuw uitvinden. Meestal zijn dat mechanische componenten zoals bijvoorbeeld een draagarm.” Of zijn onderzoek een meerwaarde is voor zijn lessen, vraag ik me af. “Absoluut. Onderzoek is altijd leren. Dat blijft. En ik vind het prettig om die opgedane kennis door te geven aan mijn studenten. Daardoor krijgen zij mee wat de laatste evoluties zijn binnen deze technologie, wat belangrijk is als ze binnen een jaar of twee op de arbeidsmarkt terechtkomen.”
"Via mijn onderzoek krijgen mijn studenten mee wat de laatste evoluties zijn binnen de technologie, wat belangrijk is als ze binnen een jaar of twee op de arbeidsmarkt terechtkomen.”
Titanium en andere dromen
Nuyts praat met passie over het onderwerp dat hem bezighoudt. Gedreven en glunderend. Er moet nog heel wat onderzocht worden, al was het maar omdat de technologie zo razend snel evolueert: “Het gaat zo hard binnen het 3D-printen met metaal. Geweldig toch dat we met onze onderzoeksgroep daarin voorop kunnen lopen?”
Neemt niet weg dat hij ook droomt van andere dingen. Een eigen productiebedrijf met deze additieve technologie, zou hij wel zien zitten. “In België zijn er nog maar weinig bedrijven die opprinten met metaal, dus zo’n eigen bedrijf uit de grond stampen… Het zou leuk zijn, moest dat kunnen in de toekomst. En als ik mij geen zorgen hoefde te maken over budgetten, zou ik mij specialiseren in titaniumonderdelen voor de lucht- en ruimtevaartindustrie. En dan zou ik niet met een kleine robot werken, maar met een die een werkbereik heeft van 5 meter, die op rails staat en die zowel in de hoogte en de breedte kan gaan… Brandstoftanks voor een raket volledig opprinten: daar is men nu al mee bezig. Kleinschalig nog, maar mocht je dat groot kunnen doen… Of vleugels en andere componenten printen voor ruimte- en luchtvaart… daar teken ik voor.”